Aumentare l'efficacia complessiva del sistema con la manutenzione connessa
Per continuare ad avere successo economico in un mondo sempre più digitalizzato, anche le aziende del settore meccanico e impiantistico devono continuamente adattare e ottimizzare i propri processi. Anche per i produttori che realizzano i propri prodotti in pre-assemblaggio, che vengono incorporati in macchine o sistemi, la priorità assoluta deve essere quella di evitare i guasti. I processi di manutenzione, o la manutenzione classica, svolgono un ruolo fondamentale in questo senso.
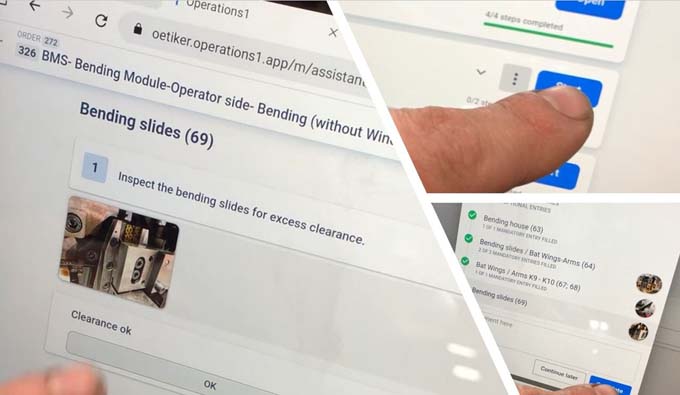
Tuttavia, in molti casi la sola implementazione di un sistema di esecuzione della produzione non è sufficiente. Occorre invece fornire soluzioni complete che non solo monitorino lo stato delle macchine, ma che semplifichino anche l'intero processo di manutenzione per i dipendenti e ne riducano il carico di lavoro.
Il Gruppo Oetiker è leader di mercato nelle soluzioni di connessione e assemblaggio. Prodotti come morsetti, clip, anelli e connettori rapidi garantiscono sicurezza, prestazioni e affidabilità nelle applicazioni di mobilità e industriali. Si trovano nelle automobili e nei veicoli commerciali, ma anche in settori come le applicazioni sanitarie e mediche e gli elettrodomestici. A causa degli elevati requisiti di qualità per l'ampia gamma di prodotti, è essenziale disporre di macchinari sempre pronti all'uso e in grado di produrre la massima qualità in ogni momento. Per raggiungere questo obiettivo, il personale addetto alla manutenzione deve disporre non solo di una pianificazione efficiente della manutenzione, ma anche di istruzioni di manutenzione specifiche per il sistema. Con la piattaforma Connected Worker Operations1 , Oetiker è riuscita a ottimizzare i processi di manutenzione esistenti.
Status quo: gli interventi di manutenzione vengono eseguiti principalmente manualmente.
Sebbene Oetiker abbia instaurato precocemente una cultura globale della produzione snella e utilizzi metodologie di base come il Visual Management, le 5S e la Total Productive Maintenance in tutti gli impianti di produzione, in precedenza mancava la completa digitalizzazione dell'organizzazione operativa. Nel 2020 è stato dato il segnale di partenza e l'azienda ha implementato un sistema MES (Manufacturing Execution System) globale chiamato Leading2Lean. Questo ha garantito la prima comunicazione tecnologica con le macchine e i sistemi, che ha fornito risposte a domande fondamentali, come i tempi di funzionamento delle macchine, i tempi di esecuzione, le interruzioni e i loro motivi, nonché i cicli di manutenzione necessari. Sebbene queste informazioni potessero essere utilizzate per impostare i periodi di manutenzione, la pianificazione dettagliata degli interventi di manutenzione doveva ancora essere effettuata manualmente utilizzando Excel, Outlook e lavagne magnetiche. Ciò comportava processi di manutenzione cartacei che richiedevano tempo e risorse, con interruzioni dei supporti e del sistema, mancanza di trasparenza e difficoltà di rendicontazione.
Le singole sfide del processo di manutenzione basato sulla carta riguardavano tre livelli in profondità: la gestione dei documenti, il livello del processo e la prospettiva globale. La gestione dei documenti, che comprende la creazione analogica, l'approvazione, la revisione, la distribuzione e l'archiviazione digitale, richiedeva molto tempo a causa dell'approccio manuale e delle interruzioni dei supporti, poiché centinaia di sistemi di Oetiker devono essere sottoposti a manutenzione con cicli diversi su base giornaliera, settimanale, mensile, semestrale o annuale. Ci sono anche variazioni di macchine per ogni sede. I processi manuali non erano in grado di mappare questa diversità su tutto il territorio, il che significava che c'era sempre un potenziale rischio di errore.
Creare un processo di manutenzione efficiente con Connected Work
Operations1 si è rivelato uno sparring partner adeguato nel percorso di digitalizzazione globale dei processi di manutenzione gestiti dai dipendenti. La scelta è caduta sulla famosa piattaforma Connected Worker grazie alle sue opzioni di integrazione con Leading2Lean, alla sua rapida implementazione e all'elevato livello di facilità d'uso. Inoltre, la soluzione software è estremamente scalabile grazie alla sua struttura modulare, al multilinguismo e alla possibilità di mappare diversi tipi di macchine utilizzando classi di struttura nel backend. Per i dipendenti del Gruppo Oetiker, l'implementazione di Operations1 significa una notevole semplificazione dei processi di lavoro quotidiani: ogni dipendente riceve ora le istruzioni di manutenzione che lo riguardano al momento giusto. Inoltre, la manutenzione viene eseguita in modo completamente digitale, utilizzando liste di controllo e protocolli di prova intuitivi, con gli operatori che eseguono le istruzioni di manutenzione passo dopo passo tramite il touchscreen del tablet. Anche le istruzioni dettagliate specifiche della macchina possono ora essere visualizzate digitalmente. Inoltre, tutti i documenti precedentemente archiviati in montagne di carta sono aggregati in un unico punto di verità a cui si può accedere a qualsiasi ora del giorno e della notte da qualsiasi luogo.
Questo riduce significativamente la complessità della manutenzione e aumenta la trasparenza grazie ai dati di processo in tempo reale e ai report generati automaticamente. Anche i guasti alle macchine possono essere evitati grazie a una migliore pianificazione e a una manutenzione regolare. Le macchine ben mantenute offrono ai dipendenti un ambiente di lavoro sicuro e moderno. Infine, ma non meno importante, un processo di manutenzione così efficiente consente una manutenzione preventiva autonoma: gli operai possono eseguire da soli piccoli interventi di manutenzione.
Aumento significativo dell'OEE grazie alla manutenzione digitalizzata
Oetiker si è posta obiettivi ambiziosi per la completa digitalizzazione della manutenzione: l'azienda mira a raggiungere un'efficacia complessiva delle apparecchiature (OEE) di 85 % nel lungo periodo. Si tratta di una cifra importante per la produttività di un impianto, il cui aumento garantisce le vendite a lungo termine. Per raggiungere questo valore, il leader di mercato si è posto dei sotto-obiettivi. "Grazie a un approccio di manutenzione digitalizzato, siamo stati in grado di aumentare l'efficienza complessiva dell'impianto nel sito canadese di 11 % dopo soli 6 mesi", afferma Jacob Reid, responsabile dell'ingegneria del Gruppo Oetiker. A ciò si aggiunge un aumento della disponibilità dell'impianto di 5 %, mentre allo stesso tempo il tempo medio di riparazione (MTTR), cioè il tempo medio di riparazione dopo un guasto a una macchina, è diminuito di 23 %.
Queste cifre parlano da sole e dimostrano che il potenziale della manutenzione digitale è tutt'altro che esaurito. Finora, 10 dei 13 siti produttivi di Oetiker in tutto il mondo sono stati implementati digitalmente e l'azienda ha già in programma l'implementazione degli altri 3 siti. "Con Operations1 stiamo definendo uno standard globale per la manutenzione preventiva nei nostri 13 stabilimenti", conferma Susanne Conrad, responsabile dell'ingegneria delle apparecchiature del Gruppo Oetiker. L'ottimizzazione dei processi di manutenzione continuerà quindi a crescere in futuro".
Fonte: www.operations1.com www.oetiker.com