Evitare le interruzioni della produzione con la manutenzione proattiva
A causa della maggiore complessità dovuta all'elevato numero di componenti integrati, il numero di percorsi di influenza nelle apparecchiature operative ad alta tecnologia aumenta fino a 10³. A causa dell'aumento della frequenza dei cicli sia nella tecnologia di azionamento che nell'elaborazione dei dati, aumenta la probabilità di un malfunzionamento causato dalla coincidenza delle ampiezze delle interferenze cicliche. Il rimedio è una compatibilità elettromagnetica completa delle apparecchiature.
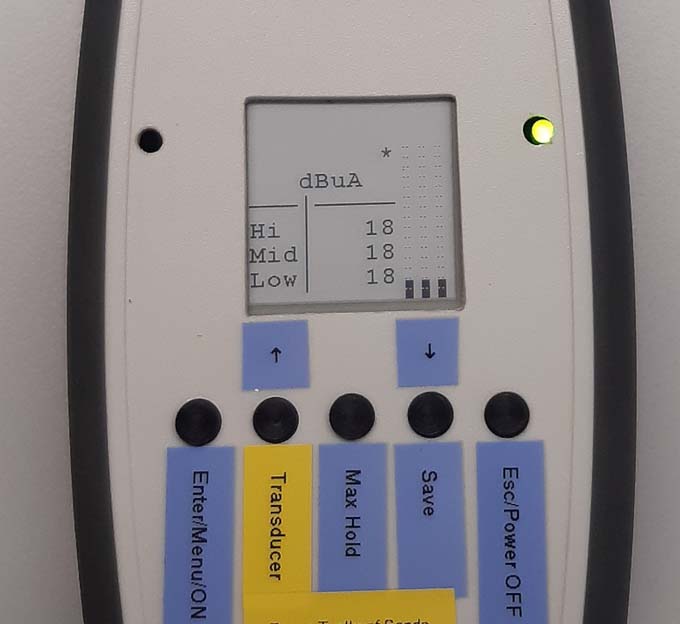
Quando sviluppano sistemi elettronici, i produttori sono spesso costretti a concentrarsi su fattori diversi dalla compatibilità elettromagnetica (EMC). Ad esempio, i componenti devono essere economicamente producibili, avere prestazioni elevate e soddisfare i requisiti dell'applicazione. Inoltre, la compatibilità elettromagnetica viene spesso testata solo in una fase successiva dello sviluppo o addirittura in fase di produzione, il che può comportare costi maggiori e ritardi se si rende necessaria una rielaborazione.
Una procedura orientata alla qualità per la CEM costruttiva e un test della CEM interna prima di immettere componenti e macchine sul mercato sono un male necessario. Ma offrono anche un grande potenziale per aumentare l'efficienza complessiva di un'apparecchiatura a lungo termine, soprattutto nella fase di utilizzo. Un software come ESMA può essere d'aiuto in questo senso. Consente un "processo di QM EMC" supportato da software che permette ai produttori e agli utenti di registrare e analizzare parametri importanti in vari punti del ciclo di progettazione e produzione con l'aiuto di un sistema di assistenza. In questo modo, i produttori di apparecchiature sono supportati nella pianificazione della costruzione e dei costi già nella fase di progettazione attraverso l'analisi dei rischi e l'uso scalabile di misure costruttive.
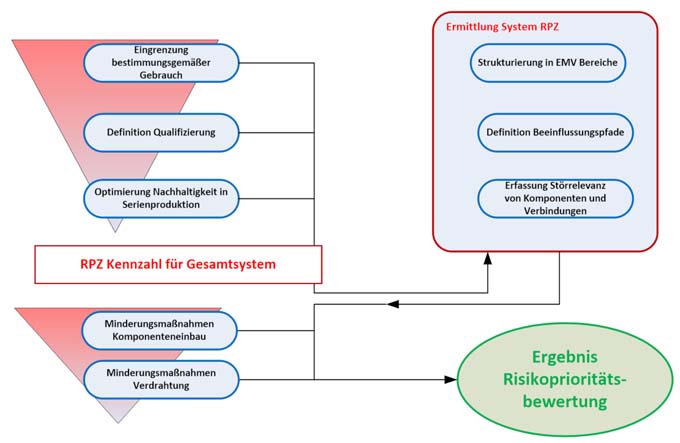
Aumento dell'efficienza produttiva grazie alle prove di tipo INTRA EMC
Le fasi procedurali della progettazione vengono interrogate passo dopo passo e le misure specifiche del progetto devono essere definite nel processo. Sulla base di questo lavoro preliminare, i fattori di riduzione della priorità del rischio vengono attivati dal database e valutati algoritmicamente in modo gerarchico. Per ogni fase procedurale, i fattori di riduzione sono memorizzati nel sistema in modo differenziato per ciascuna delle sei possibili influenze. Viene considerata la rispettiva catena di impatto, ad esempio da dispositivo (G) a dispositivo, da dispositivo (G) a linea (L) o da campo lontano (F) a dispositivo. Le oltre 400 fasi del processo moltiplicate per sei percorsi di influenza ciascuno e per tre fattori di effetto ciascuno della probabilità di accadimento, del rilevamento del guasto e della conseguenza del danno secondo la FMEA danno luogo a più di 7.000 fattori nel database e ciò dimostra l'accuratezza della priorità del rischio calcolata moltiplicando i fattori relativi al progetto.
I valori di misura rilevanti possono essere registrati anche con il metodo di misurazione LogAmp per la convalida dei parametri elettromagnetici nell'intervallo ravvicinato all'interno delle apparecchiature operative. Il vantaggio del dispositivo di misura è che può essere utilizzato in modo semplice ed economico dal personale di manutenzione senza particolari competenze in materia di EMC. È sufficiente un semplice confronto dei "valori marker" durante le prove di tipo, la manutenzione e la riparazione e con i valori target del database dell'ESMA, basato sulla norma EN 61000-4-39, con categorie di immunità definite. Ciò consente un'analisi "buona/cattiva" in loco. La curva di ampiezza e il valore equivalente registrati da un modulo logaritmico nell'unità vengono emessi come un cosiddetto "valore marcatore" per il contenuto energetico della densità di ampiezza. La misurazione viene eseguita nelle tre gamme di frequenza rilevanti per la gamma vicina (da 10 kHz a 150 kHz, da 150 kHz a 1 MHz, da 1 MHz a 10 MHz).
Evitare le interruzioni della produzione con un minimo sforzo di manutenzione
Poiché in molte aree di produzione è necessario evitare a tutti i costi un fermo macchina, le deviazioni dai parametri EM devono essere rilevate prima che si verifichi un malfunzionamento. I test EMC eseguiti a lunghi intervalli da ispettori esterni possono farlo solo in misura limitata. Si dovrebbe invece stabilire un intervallo di manutenzione separato, basato sulle probabilità di guasto predefinite dei singoli sistemi e componenti rilevanti dal punto di vista EM. In questo modo, le attività di manutenzione possono essere sincronizzate con le pause di produzione pianificate, ad esempio. Utilizzando i valori misurati del "test di tipo INTRA EMC" come specifiche target per la fase di utilizzo, è possibile per gli operatori dell'impianto effettuare un monitoraggio regolare e ravvicinato delle condizioni con l'aiuto di un sistema di assistenza digitalizzato e di dispositivi di misurazione mobili. Grazie alla migliore base dati digitalizzata, è possibile garantire una manutenzione proattiva senza interrompere la produzione a causa di malfunzionamenti imprevisti.
A tal fine, è necessario eseguire regolarmente "test INTRA-EMV" con dispositivi di misura mobili. Una variazione di un parametro EM come il campo vicino magnetico, la corrente di interferenza o la tensione di interferenza sono già indicatori di degrado o affaticamento di gruppi meccanici o elettrici, ad esempio spazzole di scarica ESD, cuscinetti dell'albero, connessioni PE, supporti di schermatura dei cavi o connessioni a vite EMC. Se le deviazioni vengono controllate regolarmente e rilevate in tempo, è possibile prevedere meglio i guasti e allo stesso tempo rendere più efficiente l'approvvigionamento dei pezzi di ricambio.
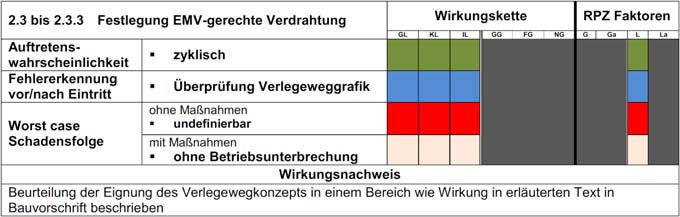
Minimizzazione dei costi del ciclo di vita nella fase di utilizzo fino all'obsolescenza
La resilienza ai guasti nella fase di utilizzo fino all'obsolescenza dipende dal degrado dei parametri EM delle misure costruttive e dei componenti utilizzati per le condizioni operative dell'apparecchiatura, come la temperatura ambiente, l'umidità dell'aria, la corrosività e la qualità dell'alimentazione. Il verificarsi di un guasto non è prevedibile in modo deterministico. Il percorso verso la produzione ininterrotta, invece, è il rilevamento di una deviazione EM, che può quindi portare a una misura di manutenzione proattiva con la specificazione di una programmazione accettabile. Un sistema di assistenza digitale costituito dal software ESMA con il sistema di misura LogAmp correlato offre al produttore e successivamente all'utente la possibilità di introdurre internamente una gestione della manutenzione RCM (reliability-centred maintenance management) e di perseguire un concetto di manutenzione predittiva nella fase di utilizzo. Ciò consente una valutazione analitica del rischio di misure di progettazione di dettaglio EM scalabili e un impegno di manutenzione scalabile con l'obiettivo di ridurre i costi di manutenzione. Allo stesso modo, è possibile garantire l'utilizzabilità a lungo termine del sistema attraverso la riparabilità dopo l'obsolescenza delle parti di ricambio originali, definendo le condizioni di installazione dell'EM per la sostituzione con componenti alternativi.
ESMA Procedura LogAmp per il concetto di manutenzione Manutenzione EMC centrata sull'affidabilità
Grazie ai setpoint EM già definiti all'interno dell'apparecchiatura in fase di progettazione, è possibile mantenere la disponibilità ed evitare l'interruzione della produzione dovuta a malfunzionamenti imprevisti applicando la procedura di misurazione LogAmp e la relativa valutazione del rischio da parte del software ESMA nella fase di utilizzo. Un modo per raggiungere questo obiettivo già durante e subito dopo la messa in servizio è l'uso coerente di un concetto di manutenzione con monitoraggio delle condizioni e brevi intervalli di manutenzione. Attraverso la valutazione algoritmica dei risultati di ogni manutenzione, viene adattato l'intervallo fino alla manutenzione successiva. Se si utilizzano le analisi preliminari dei componenti memorizzate digitalmente e integrate da una rete fitta di intervalli di ispezione, è possibile ridurre i tempi di fermo e pianificare meglio la manutenzione. Con l'aiuto di questo concetto di manutenzione, che non si basa sulle specifiche del produttore ma sulla resilienza ai guasti e sulla probabile fatica dei materiali, l'impegno di manutenzione diventa scalabile, con un conseguente risparmio sui costi a lungo termine.
A causa dei rapidi cicli di innovazione o delle catene di fornitura interrotte, non sempre è possibile procurarsi componenti di ricambio originali con parametri EM identici e non è possibile prevedere l'esatta resistenza ai guasti dopo la sostituzione. Se i parametri di interfaccia EM dei componenti e degli assiemi sono già memorizzati nel sistema di assistenza durante la progettazione o la messa in servizio, le sostituzioni possono essere organizzate in tempo utile con tempi accettabili fino alla riparazione proattiva durante le interruzioni di produzione, calcolati algoritmicamente dai risultati della manutenzione.
Autore:
Josef Schmitz è partner di J. Schmitz GmbH, un centro di competenza gestito dal proprietario per tutti gli aspetti della CEM. Il portafoglio di servizi comprende, tra l'altro, un laboratorio di misurazione accreditato per la verifica della conformità CE e una consulenza EMC competente per i produttori per quanto riguarda la qualificazione dei loro prodotti e il supporto di nuovi sviluppi. Ulteriori informazioni: www.jschmitz.de/system-emv/vollversion-esma/