IT per la produzione: il percorso verso una produzione perfetta
Che ordine state producendo al momento? A che punto è il lavoro? E quale strumento vi servirà in seguito? Mentre a queste tre domande è relativamente facile rispondere, questa è una storia diversa: Quale potenziale si nasconde ancora nelle vostre attrezzature, e non a sensazione? Conoscete i motivi più frequenti di malfunzionamento e li conoscete a menadito? Quali alternative avete a disposizione in caso di malfunzionamento e funzionano? Le risposte rapide sono fondamentali nell'attuale contesto di mercato. In questo articolo scoprirete come diventare significativi e raggiungere gli obiettivi di una produzione perfetta.
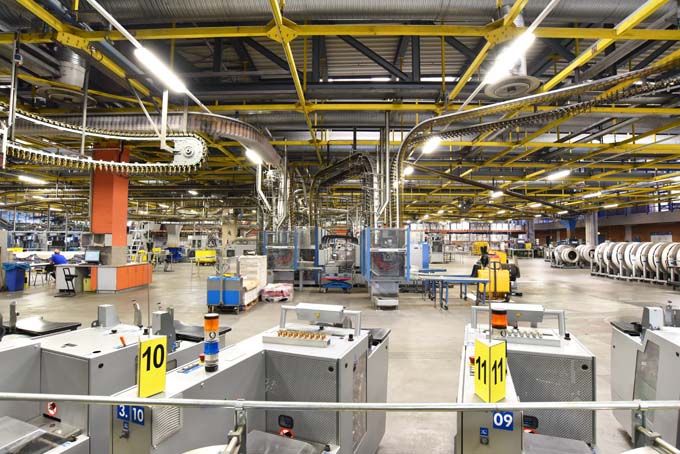
Per avere sempre la risposta giusta a portata di mano, occorre innanzitutto averne una in produzione: Trasparenza - con la semplice pressione di un pulsante. Insieme al Reattività è uno degli obiettivi primari che un'azienda deve perseguire. La trasparenza e la reattività sono a loro volta i prerequisiti per Efficienza economica - la terza variabile target del triangolo magico della produzione perfetta. Solo quando i processi di un'azienda manifatturiera possono essere controllati attraverso cicli di controllo veloci, è possibile aumentare l'efficienza economica e quindi garantire la competitività.
Piccola causa, grande effetto
Un esempio pratico illustra i collegamenti: una minuscola scheggia metallica nell'olio può causare il malfunzionamento di una pompa dell'olio. Di conseguenza, il cuscinetto viene danneggiato e causa il guasto completo di una macchina. La macchina si blocca, l'ordine non viene completato in tempo e, nel peggiore dei casi, viene imposta una penale per il superamento della data di consegna. In molte fabbriche le cose vanno ancora così.
In una produzione trasparente, reattiva ed economica, lo scenario sarebbe diverso. Il supervisore del turno dovrebbe solo dare un'occhiata al suo sistema informatico di produzione per vedere a quale macchina può passare in caso di malfunzionamento (trasparenza). Grazie al supporto del sistema, potrebbe riprogrammare gli ordini con pochi clic (reattività) e rispettare i termini di consegna (efficienza). E c'è di più: se si sfruttano le possibilità offerte dalle moderne tecnologie informatiche di produzione, la macchina non si sarebbe mai guastata. La parola magica è manutenzione predittiva. I dati di macchina e di processo registrati senza soluzione di continuità possono essere analizzati con precisione per effettuare la manutenzione proattiva delle macchine ed evitare i tempi di fermo non programmati.
Quattro elementi costitutivi di una produzione perfetta
Il caso descritto dimostra che l'obiettivo di una produzione perfetta è inevitabilmente legato alla digitalizzazione. Ma per il successo della trasformazione in una fabbrica intelligente, non è sufficiente installare le più moderne attrezzature di produzione e un sistema di esecuzione della produzione (MES). È necessario creare le condizioni quadro per un utilizzo efficace dell'informatica di produzione. Un approccio olistico è quindi dedicato ai seguenti aspetti:
- Gestione del flusso di valore 4.0
- Flussi di valore Lean
- Funzioni di supporto Lean
- Miglioramento sostenibile dei processi
Questi quattro elementi hanno dimostrato la loro validità nell'aiutare le aziende a raggiungere una produzione perfetta passo dopo passo. Il loro scopo è identificare i punti deboli ed evitarli in futuro.
Modulo 1: Gestione del flusso di valore 4.0
Il primo modulo comprende essenzialmente l'analisi del flusso di valore 4.0 e la progettazione del flusso di valore. Serve quindi a registrare, analizzare e riprogettare i processi. Oltre al processo di produzione e al flusso di materiali, si presta particolare attenzione ai flussi di informazioni e ai processi di pianificazione. Dopo tutto, essi controllano i processi di produzione in cui ogni minuto è importante. I risultati dell'analisi a 360 gradi sono presentati in un diagramma del flusso del valore. Per poter valutare rapidamente le informazioni così visualizzate, viene creato un diagramma dei tempi di consegna e viene calcolata l'efficienza del processo come misura dell'efficienza economica dell'intero processo. Per l'area dei flussi informativi e dei processi di pianificazione, ad esempio, vengono determinati il numero di strumenti utilizzati e il grado di digitalizzazione.
Ora i fatti relativi ai processi di produzione e all'ambiente di produzione sono chiari. È possibile rispondere alle domande sul processo di produzione, sul flusso di informazioni, sul processo di pianificazione e sugli strumenti (IT) utilizzati e ricavarne i passi successivi: un disegno del flusso di valore con un concetto di obiettivo e una tabella di marcia per implementare il concetto di obiettivo.
Blocco di costruzione 2: flussi di valore Lean
Il secondo modulo mira a stabilire processi di produzione snelli, ossia ad attuare in modo coerente il concetto di obiettivo sviluppato nel primo modulo. Ciò va di pari passo con l'eliminazione degli sprechi. I sette tipi comuni di sprechi, basati su Taiichi Ohno, ex direttore di produzione della Toyota e fondatore della produzione snella, comprendono: Sovrapproduzione, tempi di attesa, trasporti, lavorazioni inefficienti, magazzini, movimenti ridondanti ed errori. A questi si aggiungono la mancanza di coinvolgimento e motivazione dei dipendenti e gli sprechi causati dalle interfacce informative. Per un'implementazione di successo dei flussi di valore snelli, il coinvolgimento attivo dei dipendenti è l'elemento fondamentale.
Blocco 3: funzioni di supporto Lean
Il terzo modulo si occupa delle funzioni di supporto alla produzione, ossia della pianificazione di massima e di dettaglio e della loro integrazione nei processi produttivi. Un esempio lampante è l'ottimizzazione della pianificazione: spesso la produzione viene pianificata in modo approssimativo sulla base delle settimane di calendario nel sistema ERP. La pianificazione dettagliata dei posti di lavoro e delle macchine viene poi effettuata al giorno o al turno sulla lavagna di pianificazione nell'ufficio del caporeparto o in Excel. È evidente che la trasparenza, ma anche la capacità di reagire in termini di cicli di controllo rapidi, viene completamente meno. Poiché non si tiene conto delle capacità effettive e degli arretrati, si creano ordini di produzione o scadenze che semplicemente non sono realizzabili. Uno strumento di pianificazione integrato di un Manufacturing Execution System offre un rimedio. Supporta la creazione di trasparenza e reattività. In fin dei conti, in una produzione perfetta non devono circolare solo i materiali, ma anche le informazioni.
Blocco 4: Miglioramento sostenibile dei processi
Una volta snelliti e digitalizzati i processi, il quarto blocco consiste nell'implementare i cambiamenti in modo sostenibile nell'azienda e nel conseguire ulteriori miglioramenti. E questo avviene praticamente a margine, nella produzione quotidiana. È importante definire gli obiettivi secondo il metodo SMART e selezionare le cifre chiave giuste per misurare il raggiungimento degli obiettivi. Seguono la creazione di anelli di controllo e l'audit ciclico. In questo modo si garantisce che i processi vengano adattati tempestivamente ai cambiamenti e che, in generale, i processi di cambiamento non scompaiano di nuovo dall'agenda senza che le potenzialità siano esaurite.
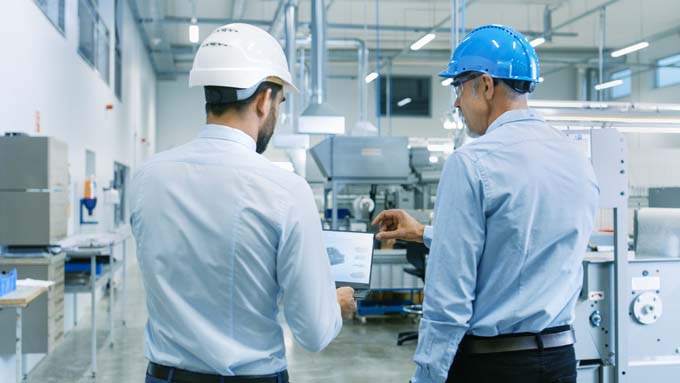
Il MES come base per la Smart Factory
Nei quattro elementi costitutivi della produzione perfetta, il Manufacturing Execution System svolge un ruolo importante come base per la Smart Factory. Infatti, se i metodi lean pertinenti sono affiancati da funzioni MES adeguate, questo è il miglior prerequisito per fare buoni progressi nel progetto. Poiché un MES registra i dati di produzione in tempo reale, è ideale per realizzare tempi di reazione brevi e cicli di controllo rapidi nella produzione. L'esempio citato all'inizio, con il truciolo metallico nell'olio e il conseguente guasto della macchina, dimostra quanto sia importante rilevare rapidamente i guasti e adottare tempestivamente le contromisure. Il prerequisito per questo è il monitoraggio permanente della produzione, dalla situazione delle scadenze allo stato delle macchine e degli utensili, fino alla disponibilità del personale e alla qualità del prodotto.
I cinque compiti MES più importanti per l'implementazione di loop di controllo veloci sono:
- Monitoraggio in tempo reale della produzione: Per registrare i dati automaticamente, le macchine e le altre periferiche sono collegate direttamente al MES tramite interfacce. Tuttavia, è possibile anche la raccolta manuale dei dati. La raccolta dei dati di officina fornisce una rapida panoramica della situazione attuale del programma, mentre la raccolta dei dati macchina fornisce informazioni sullo stato delle macchine e dei sistemi. L'operatore può vedere a colpo d'occhio nel sistema se la macchina è in funzione (verde) o no (rosso) e può reagire a un arresto senza perdere tempo. Per la pianificazione, ad esempio, sono immediatamente visibili anche le capacità del personale e le qualifiche dei dipendenti.
- Reazione a breve termine agli eventi: La gestione delle escalation consente di reagire agli eventi con breve preavviso. Oltre al già citato malfunzionamento della macchina, anche il superamento o l'abbassamento del valore limite di una caratteristica di qualità può portare alla notifica al rappresentante della qualità. Oppure il responsabile della regolazione viene informato non appena viene violato il limite di tolleranza di un valore di processo. In caso di fermo macchina, le azioni alternative possono essere rapidamente simulate con un MES e gli ordini possono essere riprogrammati con il drag-and-drop. Lo stesso vale per la pianificazione del personale.
- Calcolo e visualizzazione di cifre chiave: Nessun miglioramento del processo senza cifre chiave: un sistema di esecuzione della produzione è lo strumento ideale per calcolare e visualizzare le cifre chiave. Non solo può visualizzare le cifre chiave standard come l'efficienza, l'indice OEE o il rispetto delle date di consegna. Ad esempio, dai dati registrati è possibile determinare anche l'efficienza del processo e il tempo di lavorazione. Inoltre, i dati possono essere confrontati tra loro in diversi periodi di tempo. Ogni livello aziendale riceve le informazioni di cui ha bisogno.
- Sostegno al CIP: Il modo migliore per lavorare per evitare interruzioni o migliorare i processi instabili è con l'aiuto di un MES, in linea con il processo di miglioramento continuo (CIP). Il ciclo PDCA può essere notevolmente accelerato perché i dati sono disponibili con la semplice pressione di un pulsante. Grazie al maggior livello di dettaglio delle informazioni, è possibile scoprire più potenziale e realizzare più rapidamente i miglioramenti.
- Fornitura di dati per i sistemi ERP: Un MES riporta i dati rilevanti dalla produzione al sistema ERP di livello superiore a intervalli di tempo definiti, chiudendo così il ciclo di controllo. Sulla base di dati quali l'effettivo utilizzo della capacità produttiva, la produzione viene regolata a medio e lungo termine. Le informazioni vengono utilizzate anche per il post-calcolo commerciale e la manutenzione dei dati anagrafici.
Quando tutti e quattro gli elementi costitutivi di una produzione perfetta sono stati implementati e un Manufacturing Execution System realizza e organizza cicli di controllo rapidi, ce l'avete fatta: siete molto più vicini alle tre dimensioni target di trasparenza, reattività ed efficienza economica della produzione. Sfruttate in modo ottimale il potenziale delle vostre attrezzature, conoscete le cause più frequenti di malfunzionamento e sapete a quale macchina passare se un piccolo truciolo metallico nell'olio degli ingranaggi sconvolge la vostra pianificazione della produzione.
Autore:
Jürgen Rieger è membro del consiglio di amministrazione di Perfect Production GmbH e autore del libro di riferimento "Die perfekte Produktion. Eccellenza produttiva nella fabbrica intelligente". Perfect Production GmbH In qualità di società di consulenza, accompagna le aziende manifatturiere nel loro percorso verso una produzione perfetta e fa parte della Gruppo MPDV.