L'IA embarquée soulage le service après-vente
Les machines de production complexes sont coûteuses et constituent en même temps la base du chiffre d'affaires d'une entreprise. Selon les estimations, le coût d'une panne de machine peut s'élever à plusieurs centaines de milliers de CHF par heure[1]. Viacheslav Gromov, fondateur et directeur général d'AITAD, commente la situation en Suisse et explique comment l'IA embarquée permet de soulager les services et de créer un espace pour de nouveaux modèles commerciaux innovants.
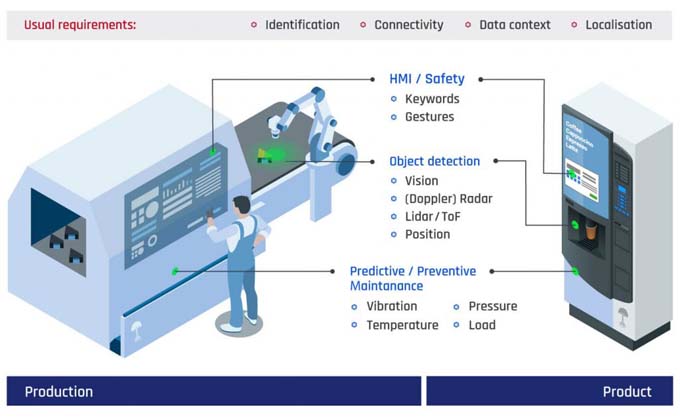
Les constructeurs de machines misent sur un entretien régulier pour s'assurer que les machines fonctionnent, que la qualité et le débit sont corrects. Les intervalles d'entretien réguliers nécessitent toutefois beaucoup de personnel - et il n'est pas toujours facile de trouver du personnel qualifié. Et toutes les interventions ne sont pas nécessaires : si la machine fonctionne sans problème, la visite du technicien de service est en fait une perte de temps.
Réduire les intervalles de service
Par le passé, les intervalles de service réguliers étaient indispensables - mais ne garantissaient pas pour autant qu'une machine ne s'arrête pas soudainement. En effet, même pour un personnel hautement qualifié, il n'était pas possible de détecter toutes les pannes qui s'annonçaient déjà.
C'est là que l'intelligence artificielle entre en jeu. Des capteurs permettent de surveiller les machines en continu (Predictive Maintenance). Cela génère de grandes quantités de données qui peuvent en dire long sur l'état de santé de la machine ou de certains composants. Si l'on fait évaluer les données des capteurs par une IA, il est possible de prévoir longtemps à l'avance les éventuelles pannes. Cela signifie une situation gagnant-gagnant aussi bien pour le fabricant que pour l'utilisateur : les pannes imprévues n'apparaissent plus malgré la réduction des intervalles de service.
La plupart des solutions d'IA actuellement disponibles sur le marché nécessitent toutefois une grande capacité de calcul et dépendent d'une infrastructure réseau performante et coûteuse. Les données des capteurs sont alors transmises via le réseau, analysées sur des serveurs centraux ou dans le cloud, puis le résultat est renvoyé. Cela ne coûte pas seulement du temps, mais pose aussi la question de la sécurité des données. Il est bien sûr dans l'intérêt compréhensible du fabricant d'avoir accès à ces données - reste à savoir si les clients qui utilisent les machines veulent que des données de processus éventuellement sensibles soient transmises via Internet.
Les solutions d'IA ne doivent pas être compliquées et coûteuses
Des capteurs modernes, et pourtant peu coûteux, permettent désormais de collecter des données de l'ordre du giga-échantillon. Avec une telle quantité de données - on atteint vite un volume de plusieurs téraoctets, surtout si les données de plusieurs machines doivent être analysées - une transmission en réseau n'est pratiquement plus possible, même avec un câblage direct en fibre optique. C'est pourquoi il est non seulement plus habile, mais aussi nettement plus économique d'effectuer l'évaluation des données directement sur place, dans l'appareil.
Une telle surveillance locale n'est toutefois possible que depuis quelques années. La capacité de calcul croissante des semi-conducteurs, même les plus petits, permet de placer le capteur et l'IA directement sur une petite carte électronique adaptée à l'emplacement de montage. Le capteur n'envoie alors plus ses données via le réseau, mais directement à l'IA sur le même circuit imprimé. L'IA "regarde" chaque fragment de données dans la mémoire de travail (RAM), les évalue et rejette ensuite les données brutes du capteur. Seuls les résultats de l'évaluation sont transmis - dans le cas le plus simple, par une lampe sur l'appareil qui s'allume en rouge en cas d'apparition d'une erreur. Ou bien le service après-vente est directement informé qu'un composant ou l'ensemble de l'appareil présentera une erreur dans un délai déterminé. Le service peut alors commander les pièces de rechange nécessaires et planifier avec le client une date de maintenance qui n'entrave pas la production.
De tels systèmes d'IA locaux sont appelés "IA embarquée". En raison des limites de ressources imposées par le système, ces systèmes sont relativement peu coûteux sans pour autant perdre de leur robustesse. Ils n'entraînent pas de coûts ultérieurs tels que ceux engendrés par une infrastructure de réseau et sont en outre capables de fonctionner en temps réel, ce qui leur permet d'être utilisés dans des environnements critiques en termes de sécurité.
Quelles sont les possibilités d'utilisation de l'IA embarquée ?
Même si les possibilités d'utilisation de l'IA embarquée sont presque illimitées, nous allons présenter ici une (petite) sélection de cas d'utilisation potentiels :
- Dans les moteurs, les arbres d'entraînement peuvent être surveillés à l'aide de capteurs à ultrasons. Si des anomalies apparaissent dans l'image ultrasonique, indiquant une possible défaillance, l'IA le détecte.
- Les pompes et les tuyaux peuvent également être surveillés par l'IA, ce qui permet de voir très tôt si un tuyau va se fissurer par exemple. L'IA peut même détecter si, par exemple, la lessive originale ou un substitut s'écoule dans le tuyau.
- Les axes et les amortisseurs peuvent être surveillés par exemple à l'aide de capteurs de pression, de vibrations ou de bruit.
- L'usure des bandes transporteuses peut être détectée à un stade précoce grâce à la spectrographie
- Surveillance des principaux composants en panne et/ou des pièces d'usure dans les machines
- Surveillance des systèmes de refroidissement et des éléments chauffants
Garantie de panne malgré un service réduit et gagnant-gagnant pour le fabricant et le client
Pour le service après-vente, la maintenance prédictive signifie que les intervalles de service peuvent être réduits et les visites "inutiles" évitées, et que la planification des travaux de maintenance peut être nettement plus flexible. Les fabricants de machines peuvent garantir une grande sécurité contre les pannes avec moins de personnel de service.
Ces nouvelles possibilités de maintenance prédictive ouvrent "en passant" d'autres potentiels pour le constructeur de machines. Outre la réduction du service, il est possible de garantir la sécurité contre les pannes ; ce scénario se prête également à l'exploitation d'un nouveau modèle commercial : louer des machines au lieu de les vendre. L'intérêt pour l'obsolescence diminue, car une durée de vie aussi longue que possible devient un avantage commercial pour le fabricant. Pour le client aussi, cela présente des avantages : l'achat de machines ne devient pas un investissement unique important et pèse moins sur la trésorerie.
En ces temps de pénurie de personnel et d'efforts de durabilité, les constructeurs de machines peuvent faire d'une pierre plusieurs coups avec l'IA embarquée et se construire une autre USP. Ils deviennent ainsi des partenaires fiables à long terme et se démarquent en même temps des produits de masse, par exemple en provenance d'Asie.
Auteur :
Viacheslav Gromov est le fondateur et le directeur général de AITAD. Il développe une intelligence artificielle liée à l'électronique (IA embarquée) qui effectue des tâches définies localement et en temps réel dans des appareils et des machines. Il est l'auteur de nombreuses contributions ainsi que de divers manuels dans le domaine des semi-conducteurs.