Libérer le potentiel du numérique dans la fabrication moderne
L'étude "Zukunft Industrie" de Staufen désigne l'excellence numérique comme l'une des quatre dimensions de la compétitivité et la base élémentaire d'une entreprise durable, capable de se transformer et de résister. L'immobilisme est un frein et seul le progrès promet le succès et la croissance à long terme - les entreprises de production n'échappent pas à cette règle.
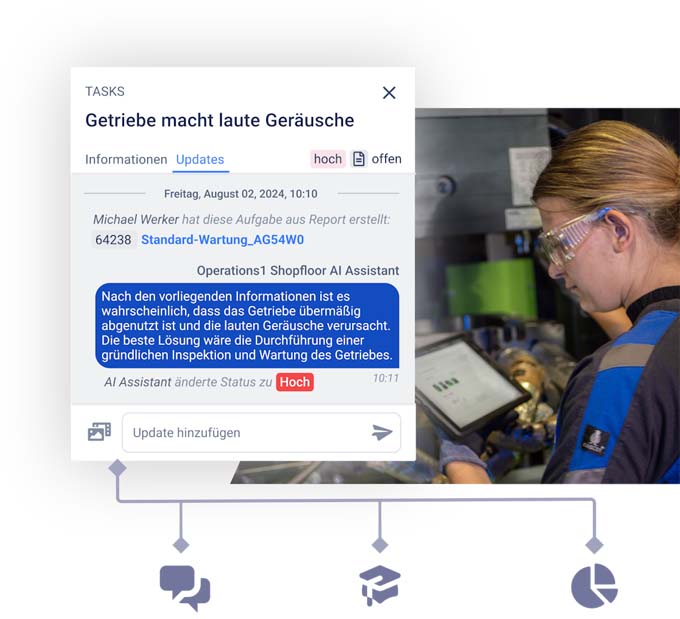
Même si la numérisation, et a fortiori l'introduction de l'IA dans la fabrication moderne, sont encore relativement lentes, des exemples pratiques présentés dans le cadre de l'événement Future Manufacturing d'Operations1 montrent comment les entreprises industrielles peuvent aujourd'hui profiter de technologies avancées et de stratégies de fabrication intelligentes. Dans ce qui suit, j'aimerais donc résumer quelques-unes des principales conclusions et en déduire comment la numérisation dans la fabrication peut être poussée plus loin à l'avenir.
Où en est la numérisation dans la production ?
Il y a quelques années encore, Industrie 4.0 était le grand mot d'ordre. Selon un rapport d'étude de BitKom datant de 2022, 90 % des entreprises interrogées voulaient utiliser à l'avenir des applications pour l'industrie 4.0 ou prévoyaient de le faire. Une enquête actuelle de Staufen sur la numérisation en 2024 prouve toutefois que la majorité des entreprises en principe disposées à mettre en œuvre ces plans ne le peuvent pas ou ne le font que lentement en raison d'un manque de ressources en personnel (58 %) et de données non structurées (53 %). Pourtant, les conditions sont en principe réunies, car le marché offre désormais de nombreuses solutions différentes qui soutiennent numériquement les domaines les plus divers de l'entreprise - même sans grand investissement en personnel.
Faire avancer la numérisation des processus de l'atelier avec des solutions innovantes
ProMinent GmbH est un bon exemple de la raison pour laquelle il est urgent de traduire les flux de travail traditionnels en processus numériques, surtout lorsque les ressources humaines internes sont limitées. Auparavant, le fabricant de techniques et de pompes de dosage travaillait avec des cartes d'erreur analogiques. Christian Braun de ProMinent décrit l'ancien processus comme très long. Les collaborateurs devaient d'abord chercher les codes d'erreur sur des listes A4 avant de pouvoir remplir les cartes. S'y ajoutait une carte d'accompagnement qui devait être agrafée au produit concerné. Cependant, tous les collaborateurs n'effectuaient pas toujours cette tâche au même moment, certains d'entre eux collectant même des données tout au long de la semaine pour les inscrire ensuite d'un seul coup à la main - et donc souvent de manière incorrecte. Les fiches d'erreur parvenaient ensuite au collaborateur suivant, qui devait saisir manuellement les résultats dans Excel. D'autres listes Excel sont venues s'ajouter en cours de procédure. Beaucoup de travail donc, qui a pris beaucoup de temps aux collaborateurs.
Pour la gestion de la qualité, ProMinent a donc prévu d'introduire des listes de contrôle numériques, des instructions de travail et des cartes de collecte des erreurs, qui permettent de tout regrouper sur une interface numérique en réseau. Pour chaque code d'erreur, il n'y a plus qu'une seule carte d'erreur correspondante, et la carte d'accompagnement est remplacée par un code QR que l'ouvrier doit simplement coller. Toutes les données sont ensuite rassemblées dans notre plateforme Connected Worker et, grâce à la connexion SAP, il est également possible d'établir directement une évaluation numérique.
Lors de l'introduction de processus numériques, il est particulièrement important d'aller chercher les collaborateurs dès la première étape et de leur présenter le futur processus de manière compréhensible. Même chez les ouvriers de longue date, le scepticisme initial a rapidement cédé la place à un grand enthousiasme après la démonstration de la procédure de numérisation, pratique et permettant de gagner du temps.
Des processus standardisés et des solutions cloud pour plus de flexibilité
Les avantages de la numérisation sont particulièrement visibles dans le contrôle qualité. Chez Quantum-Systems GmbH, fabricant de drones de reconnaissance, entre autres, le passage au numérique était inévitable, car l'augmentation des volumes de vente et la croissance rapide des effectifs ne permettaient plus d'assurer le traitement des commandes avec la qualité habituelle. De plus, la production est soumise à des exigences particulières, car chaque pièce montée doit être clairement identifiable par son numéro de série. Un acte qui était auparavant consigné sur papier et scanné de manière compliquée. La numérisation a permis de créer des instructions de travail faciles à suivre, qui permettent aux nouveaux collaborateurs de se lancer dans la production avec une phase d'apprentissage nettement plus courte. Globalement, la numérisation a rendu les processus plus transparents et compréhensibles à tout moment, ce qui a permis à Quantum-Systems de se qualifier pour la certification EN9100, importante dans le domaine de l'aérospatiale. Comme toutes les instructions sont disponibles sous forme numérique dans le cloud, les adaptations sont en outre possibles rapidement et de manière globale. Il est ainsi possible de réagir à tout moment et de manière flexible aux souhaits et aux modifications des clients.
L'intelligence artificielle comme avantage concurrentiel
Outre la numérisation classique, la production intelligente, c'est-à-dire l'utilisation de l'intelligence artificielle, joue un rôle de plus en plus important. De plus en plus d'entreprises sont invitées par leur direction à mettre en œuvre des améliorations par l'IA dans tous les départements. Les possibilités de l'IA de faire des prévisions et d'en déduire des recommandations d'action offrent de nouveaux potentiels aux entreprises de fabrication dans de nombreux domaines - et ce, du traitement des commandes au contrôle de la qualité. Néanmoins, les entreprises traditionnelles se demandent comment faire.
Il n'est pas toujours nécessaire de lancer un projet d'IA à grande échelle. Notre assistant d'atelier AI, qui s'intègre parfaitement dans notre plateforme Connected Worker, est un exemple de la manière dont l'IA peut être intégrée facilement et surtout de manière judicieuse dans les chaînes de processus existantes. Il permet aux entreprises d'organiser et d'automatiser les processus de manière encore plus efficace.
Renforcé pour l'avenir de la fabrication
L'utilisation de l'IA sur le shopfloor permettra à l'avenir de résoudre de nombreux problèmes et, grâce à des technologies telles que l'apprentissage automatique et la vision par ordinateur, d'améliorer les interactions entre l'homme et la machine. Cela augmente la sécurité sur le lieu de travail et permet aux collaborateurs de se concentrer davantage sur les activités à valeur ajoutée.
L'industrie de la fabrication se trouve à un tournant et celui qui n'ose pas aller de l'avant maintenant se fera distancer à plus ou moins long terme. C'est pourquoi Lena Weirauch, CEO & Co-Founder chez ai-omatic solutions, recommande d'oser se jeter à l'eau, car les obstacles à l'utilisation de l'IA générative n'ont jamais été aussi faibles. Les décideurs du secteur de la fabrication doivent comprendre à quel point l'intégration de technologies avancées telles que l'IA, les solutions en nuage et les outils de transformation numérique est critique pour l'avenir de l'ensemble du secteur. Ces technologies ne sont plus des visions lointaines, mais des outils concrets qui créent dès aujourd'hui des avantages concurrentiels et améliorent l'efficacité industrielle. On sent que la peur des nouvelles technologies s'estompe peu à peu pour laisser place à une acceptation pragmatique et ciblée. Cela reflète une tendance globale qui gagne en importance au-delà des frontières industrielles.
À propos de l'auteur : Benjamin Brockmann est CEO et cofondateur d'Operations1 depuis 2017. Il a étudié de 2014 à 2016 à l'Université technique de Munich et a fait de la recherche avec ses cofondateurs à l'Institut Fraunhofer, où il a également obtenu la base du contenu de la fondation grâce à son mémoire de master sur les systèmes d'information des ouvriers. Il a également acquis de l'expérience chez KPMG dans le domaine du conseil en informatique et en finance, ainsi que chez Arthur D. Little dans le domaine de la stratégie, de l'innovation et de la technologie. Pendant son temps libre, il aime utiliser sa licence internationale de pilote privé pour voir le monde d'en haut et jouer au tennis. Pour en savoir plus, voir www.operations1.com.