Traceability program: transparency for outdoor articles
The well-known manufacturer of outdoor articles Tatonka focuses on more transparency: With the new traceability program, all manufacturing and transport steps of each individual product can now be tracked online.
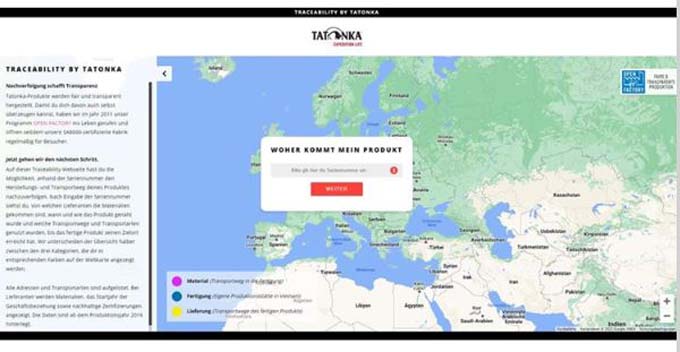
For Tatonka, a manufacturer of outdoor articles, sustainability and transparency have long been important issues. As part of its "Open Factory" program, the company has been inviting people to visit its SA8000-certified factory in Vietnam since 2011. Every Friday, the factory opens its doors to visitors. Now the manufacturer is going one step further and launching a comprehensive traceability program to make all stages of the manufacturing and transport process transparent.
View manufacturing and transport routes
And this is how it works: On the Traceability website Tatonka, all owners of a product from this company can trace the origin of the individual material components up to the sewing thread and the complete manufacturing and transport route as well as the respective means of transport by means of the serial number on the label. All products from all product groups from 2016 onwards can be viewed in this way. After entering the serial number, a world map with a detailed index shows in detail from which suppliers the materials used in each case originate and which sustainability certificates the manufacturers can present. The address is also disclosed, as is the start of the business relationship.
From the suppliers, the materials make their way to the plant in Vietnam. Here, too, it is possible to see which route they have taken and by which means of transport. Production takes place at the Mountech plant, after which the finished product begins its journey to its destination, traceable in all stages, again showing the transport route and means of transport, for each individual product delivery.
Keeping your finger on the pulse with traceability program
According to Tatonka, all steps from material purchasing and manufacturing to the transport of finished products are in the company's own hands and are efficiently controlled. The consolidation of transport routes, both for deliveries from various material manufacturers to a central warehouse and the filling of two production lines from this central warehouse, and for the central export of all manufactured products in one container, reduces resource consumption and cuts CO2 emissions. Thanks to the new traceability program, the family-owned company from Dasing, Germany, is willing to be watched.