Networked industrial workers: 6 levers for more productivity
In industry, the focus is shifting away from machines and towards people. This is mainly due to the worsening labor shortage. The aim is to deploy personnel as intelligently and flexibly as possible. AI plays an important role in this. Industrial software expert Augmentir shows 6 possible approaches.
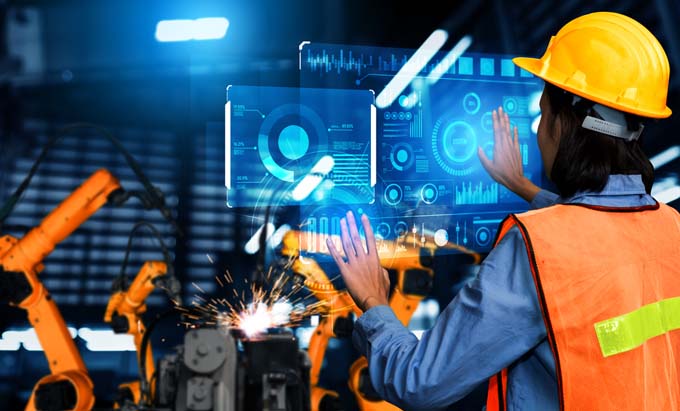
The digitalization initiatives of recent years have been shaped by Industry 4.0 and the communication of sensors and systems. Now the shortage of skilled workers is shifting the focus to human resources. Based on studies and the software manufacturer Augmentir's own project experience, 6 developments are currently emerging here:
1. skill management has an increasing impact on production
According to a study conducted by management consultants Mercer in spring 2023, companies are increasingly investing in skills management solutions that record skills and qualifications. But this is only the first step: from 2024, the main focus will be on optimally deploying skilled and unskilled workers based on their documented skills - from one day to the next if necessary. It will also become more important to provide them with individual guidance and support at their workplace. AI algorithms will provide the necessary personalization.
2. urgent transfer of knowledge
In its current study "HR Trends in the Food and Consumption Chain", the Arbeitgebervereinigung Nahrung und Genuss e.V. (ANG) emphasizes: "In view of the increasing number of baby boomers leaving the workforce, ensuring an orderly transfer of knowledge is becoming increasingly important." Mentoring programs or partnerships between older and younger employees can help with this. However, such mentors are not always and everywhere available on site to take the new employee by the hand. This is where digital remote assist systems can help. They enable industrial workers to chat and consult with experienced experts from the factory floor. As a welcome side effect, the protocol builds up a knowledge database that survives any employee turnover.
3. trainings become measurable
The concrete benefits of training measures carried out have so far been difficult to grasp. Long-term evaluations were not carried out in many places for cost reasons. Until now. For teams in production, the effectiveness of training can now be measured technically - almost incidentally, during their shift. Smart algorithms not only help to analyze the data of individual work steps and thus evaluate progress through further training. They also indicate measures with the greatest potential for improvement and suggest targeted training opportunities for different teams.
4. gaps in maintenance management are closing
Although computerized maintenance management systems (CMMS) help with the planning of maintenance tasks and the tracking of work orders, they only do this to a limited extent. This is because daily maintenance routines, which are not carried out by maintenance specialists but by machine operators, fall through the cracks in these systems. Yet it is precisely these routines that play a key role in determining the service life and functionality of a system in the long term. Connected Worker tools provide easy-to-understand instructions for this. This turns the vision of "Total Productive Maintenance" into reality.
5 Chatbots reach the store floor
Ever since the hype surrounding ChatGPT, companies have been looking at the potential uses and benefits of generative AI. A recent study from the customer service department of a software manufacturer shows that employees who had only been with the company for two months were already acting like employees who had been on board for six months thanks to the AI helper. More and more of these chatbots are also helping to answer staff's spontaneous questions in production and maintenance. For this to work, however, it is crucial that the bot recognizes whether it is talking to an expert or a temporary employee. This allows it to adjust the level of the answer as well as its level of detail and confidentiality according to the role.
6. quality management starts in production
Employees in production and maintenance are increasingly becoming a central part of the quality management process. After all, if quality and safety incidents can be identified at this early stage, problems can be investigated more quickly and proactively addressed in good time. This increases occupational health and safety and reduces the costs of poor quality. Studies also confirm this. According to a study by analyst firm LNS, equipping the frontline workforce with networked technologies is currently the most important lever for collaborative quality management for leading companies in the area of Quality 4.0.
"Thanks to digitalization, the importance of the operational workforce is becoming more and more prominent," emphasizes Russ Fadell, CEO of Augmentir. "Tasks that frontline workers used to do more or less on the side are becoming visible and measurable thanks to digital tools. Be it autonomous maintenance or identifying and rectifying quality problems: Connected worker technology fully demonstrates the value contribution of the men and women in blue overalls. In short: it really puts people at the center."
Source: www.augmentir.com