Laser vibrometry: measuring vibrations from product development to quality assurance
Analyzing vibrations in components, products or systems not only provides valuable insights for research and development, it also offers potential for improvements in quality assurance in production. As a non-contact measurement method, optical laser vibration measurement allows an unadulterated view of the vibrations. Scanning vibrometers even make it possible to analyze the vibration amplitudes of any surface.
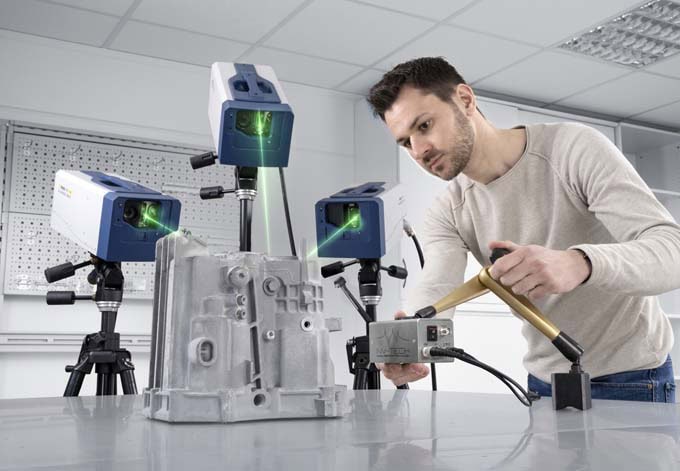
If solid materials are subjected to mechanical stress or electrical excitation, they deform and begin to vibrate to a greater or lesser extent. These vibrations depend on the shape, the material, the excitation and many other factors. Laser vibrometers are used to measure and analyze the vibrations without contact. These are used to evaluate different design variants during development and to optimize products. However, deviations in vibration behavior can also indicate faults in the product during production.
Range of application of laser vibrometry
In vibroacoustic quality testing, a laser Doppler vibrometer scans objects for vibrations precisely and without contact on practically all surfaces (image above). Measurement data such as frequency response and resonance frequency, impulse response and data on damping properties are obtained. The optical measurement with laser light produces a map of the amplitude distribution of the vibrations without influencing the measurement object, e.g. through contact or mass loading (as with accelerometers). The method is suitable for almost any vibration-related problem in research, development, production and condition monitoring or quality assurance and for objects of different sizes: from entire car bodies, large aerospace parts, motors and actuators to micro components such as MEMS or biomedical samples and components in the micrometer range. Depending on the task and sensor design, vibrations up to the GHz range can be detected or, as with the new VibroScan for surface scanning, frequencies up to 32 MHz can be recorded fully digitally.
Optimize desired oscillations
Vibrations are not undesirable everywhere. We all appreciate the vibrating alarm in cell phones or use electric toothbrushes. In many applications, it is important to find the best product design so that vibrations fulfill their purpose optimally. This is where scanning vibrometers are used, which create an areal vibration analysis. Applications in industry include vibrating conveyors or control and operating panels. High-quality packaging systems and industrial joining processes that use ultrasonic welding can also be developed more quickly or checked and optimized during operation with the help of a vibration analysis. Another application is the "vibration transport" of liquid droplets, for example in medical analysis. However, vibration analysis is also a reliable method for developing high-quality products for consumer goods: The vibration of a loudspeaker membrane, which provides the sound of a loudspeaker box, can be analyzed and improved. There are also a large number of less obvious applications such as fans, computer housings, medical products and structure-borne noise and therefore vibrations also play a major role in production systems.
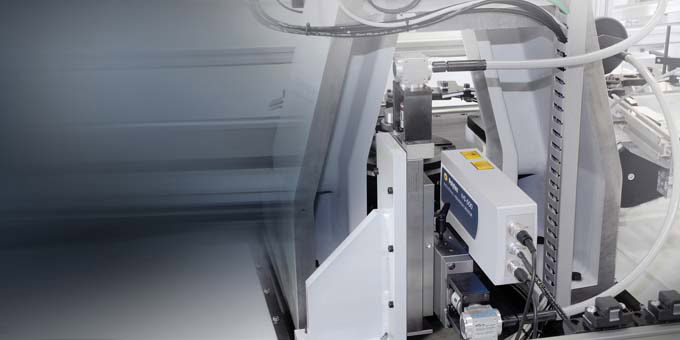
Minimize unwanted vibrations
Deviations in the vibrations of an object from the target specifications allow conclusions to be drawn about the smooth running of drives, manufacturing deviations in production, incipient bearing wear and many other faults. This is where vibrometry can be used inline for quality assurance. The prerequisite is that the sensor can detect and evaluate vibrations quickly and precisely and that the measuring system can be integrated into a production system as easily as possible. Polytec's vibrometers support various interfaces such as COM/DCOM, offer an internal macro language and provide an API for programming. The measurement data is usually transmitted via TCP/IP Ethernet. Polytec also offers extensive tools and examples to ensure smooth integration.
Measuring deviations, but where?
If vibration measurements are used for quality control, the following questions arise: Where can precise measuring points be found for reliable quality assurance in order to identify deviations and minimize rejects? Which conclusions can be drawn from which surface based on deviations? Laser Doppler vibrometers provide good indications here, even during the development of the intended test method: The best measuring points and surfaces can be found as early as the development stage to indicate the specific properties or possible defects through their vibration behavior. This allows measurements to be taken at a meaningful maximum amplitude point, which saves time during commissioning and ensures meaningful quality data on the products.
Improve signal-to-noise ratio
In practice, measuring surfaces are usually optically rough. This means that the light is not only reflected, but also scattered. It contains dark and light areas, so-called speckles. This effect leads to fluctuations in light intensity at the photodetector and, in optical measurements, to broadband noise and unwanted signal dropouts. Therefore, several measurements or a high number of averages are often necessary for a good result. Polytec solves this problem with QTec technology, which uses multiple photodetectors to drastically improve the signal-to-noise ratio. For this purpose, QTec vibrometers use an innovative multi-channel interferometer with receiver diversity. It bundles the best measured values from different perspectives and recombines them for a consistent measurement result. Each detector is an observer of the measuring point with its own perspective and sees its own random speckle pattern (image below). The combination of the signals from the spatially distributed detectors then automatically results in a statistically stable signal level for each individual measurement, regardless of the measuring surface. With this new method, measurements can be taken up to ten times faster, as one measurement is sufficient and no further averaging is required.
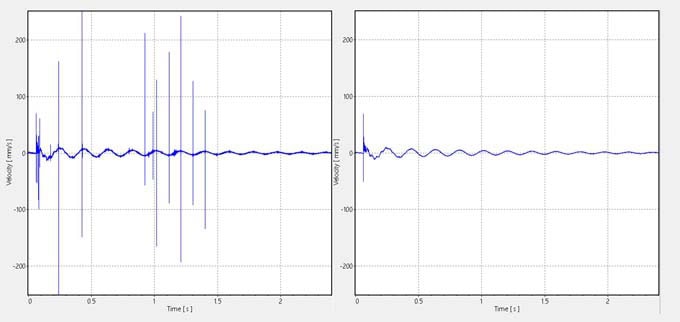
New measurement options
To measure both large and very small parts in the shortest possible time, RoboVib® combines a fully automated experimental modal analysis with VibroScan QTec Xtra 3D. The scanning vibrometer is mounted on a robot arm and moved over the object, e.g. a vehicle body. This reduces the testing time, even for complex 3D components, from days or even weeks to just a few hours thanks to comprehensive 360° measurements. For smaller parts, RotoVib automates® experimental whole-body modal analysis since 2024. Here, the test object rotates around its own axis on a turntable. Automatic repositioning allows the test object to be measured automatically from all sides. Thanks to the effortless set-up, users also save valuable measuring time here.
If measurements are to be taken through a layer of water for certain applications, the wavelength of the laser must be adapted to the water medium. Polytec's latest product, VibroScan QTec Neo, offers a HeNe laser in the measuring head whose wavelength is not absorbed by water. This means that sound field analyses of hydrophones (underwater microphones) or components of medical ultrasound applications can now be carried out under water for calibration purposes just as easily as in air. Here too, QTec technology drastically shortens the measurement time by minimizing dropouts.
On-site measurements, for example by a service provider, also require compact measuring devices that are easy to transport and install. The modern VibroScan systems for area measurement are on average around 50% smaller than the 1D predecessor models. This means that the measuring device can also travel as luggage, especially when traveling by air. AI functionality is also incorporated into the vibration measurement thanks to the associated PSV software (Polytec Scanning Vibrometer). This increases user-friendliness and reduces the set-up time for the measurement, for example through automatic object recognition and 3D adjustment. This also significantly reduces the amount of training required by the user.
Source and further information: Polytec