Individual sensor solutions often cheaper than conversions
In special machine construction or when converting, upgrading or retrofitting existing machines and systems, commercially available sensors often do not fit in the intended position. This can be remedied by a service from sensor specialist burster.
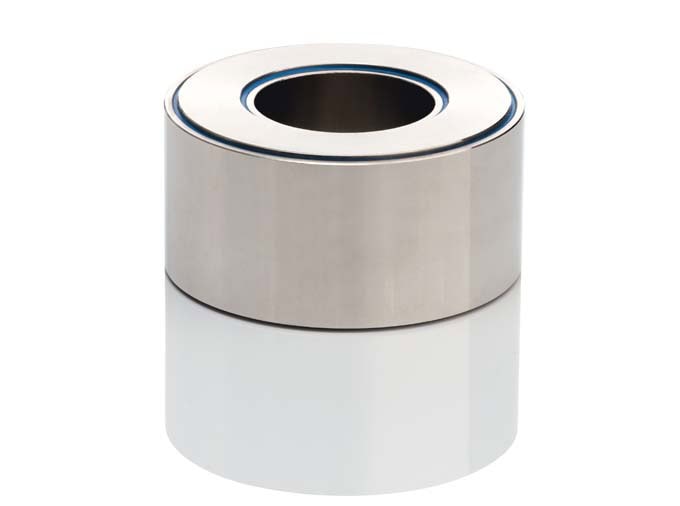
The German company burster from the Black Forest focuses on supplying users in mechanical and plant engineering, automation, automotive engineering with suppliers, electrical engineering, electronics and the chemical industry. With the MySensor service, all force, torque, displacement and pressure sensors from the portfolio can be adapted to the user's specifications or redesigned to meet individual customer requirements. Although this may sound time-consuming, it is usually cheaper than converting the systems themselves for the use of standard sensors, according to the company. The procedure also saves time and guarantees optimum measured values, the company adds. The conversion begins with a feasibility analysis in which CAD data is evaluated. If necessary, the sensor experts inspect the device via video in order to find the best possible position for force or torque measurement and then agree on the procedure. After the analysis, a prototype is produced, tested and evaluated by the user and then manufactured in series. The materials available are aluminum or stainless steel. They cover a wide range of application requirements and are suitable for special requirements in areas such as hygiene or medical technology. If required, strain gauges can also be integrated directly into customer parts to absorb forces.
Special design cheaper - how does that work?
Custom-made products are cost-intensive and therefore undesirable. However, it is often sufficient to adapt the sensor design in order to avoid a mechanical conversion of the machine. This saves time and money. The range of possibilities is wide: housing variations with modified inner or outer diameters, shoulders or flanges or recesses on the housing, modified (through) holes for countersunk screw heads are sufficient in some applications for the sensor to fit. Sometimes fully encapsulated sensor bodies are required to prevent the ingress of foreign particles during injection molding (image above). One example can be found in motor vehicles, where a sensor with a particularly flat design is required for force measurement on the control pedal. But even more complicated applications can be implemented quickly with MySensor. Determining the center of gravity of a crane boom truck requires insensitivity to vibration and shock as well as integrated low-power electronics and maximum reliability thanks to a fully encapsulated, laser-welded design. The insensitivity to lateral loads is ensured by eight strain gauges. Another complex application example can be found in the measurement of intraocular pressure. Here, small forces have to be measured with low temperature drift (image below), which was achieved by decoupling the sensor body of the "contact glass dynamometer".
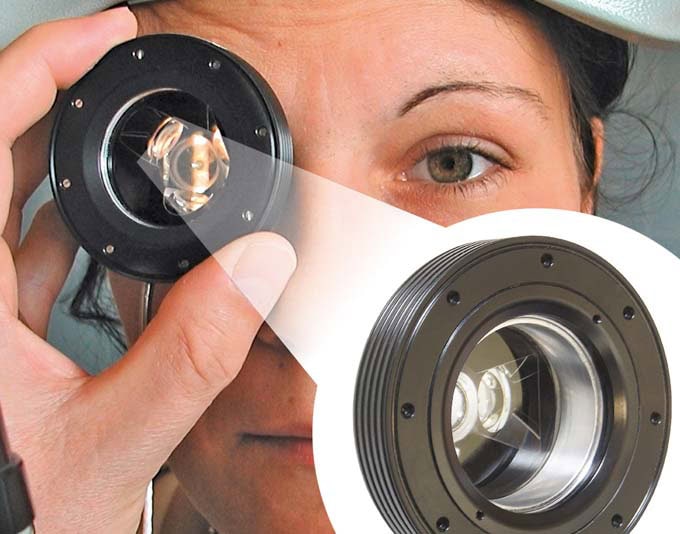
Source and further information: www.burster.de