Digital retrofit integrates legacy systems into modern workflows
Who doesn't dream from time to time of being able to digitize their machine and plant parks without legacy costs, on a greenfield site, so to speak? In most cases, this remains a dream. In reality, it is mostly a matter of converting a wide variety of systems into digitized workflows. Six application scenarios illustrate what a digital retrofit can look like.
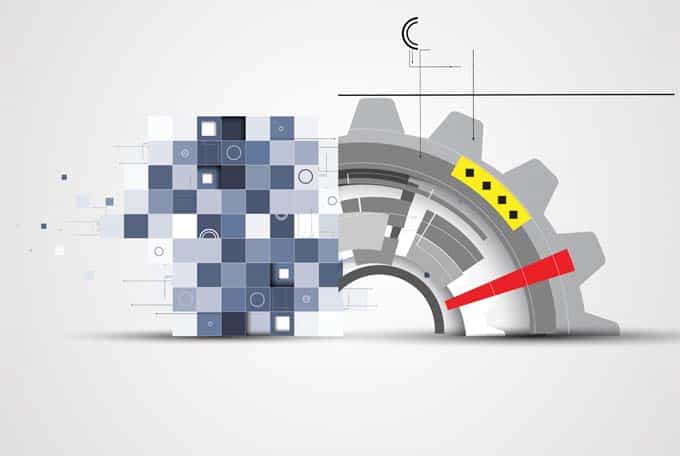
Digitization is in full swing - and no one can escape it. One of the biggest stumbling blocks in the industrial environment is the integration of legacy systems (digital retrofit). This is because these systems lack two important prerequisites in particular: the sensor technology to capture data and the data interfaces to forward it. Without these capabilities, however, it is not possible to optimize planning and changeover times, increase performance and availability, improve quality tracking and tracing, or implement predictive maintenance.
Digital retrofit as a solution
A digital retrofit, often referred to as Retrofit 4.0 in reference to the hype term Industry 4.0, therefore consists of equipping legacy systems with the necessary sensor and control technology - and this during ongoing operation, without break or downtime. Another complicating factor is that these are usually special individual cases. "One size fits all" is practically impossible with retrofits. Sensor-communication retrofitting therefore requires a careful, application-related inventory and feasibility analysis in each case. The possible application scenarios for digital retrofits are wide-ranging.
Six application scenarios
LeanBI, a specialist for data science applications headquartered in Bern, describes six typical scenarios for practical use and the potential positive effects:
- Intralogistics: Booming online retail is leading to a rapid increase in shipping volumes and thus to high utilization of logistics facilities, which are also unable to keep pace with this growth due to their (partially) analog structure. However, additional buildings or plant complexes cannot be realized as quickly as retrofitting existing facilities. It is therefore the faster as well as more cost-effective and resource-saving way. In addition, it can also increase the service life of the plant.
- Assembly linesFor many product suppliers, such as automotive suppliers or bicycle manufacturers, meeting delivery times is becoming increasingly challenging due to the high demand and the growing number of variants. In the event of the smallest failure in the production chain, the entire plant comes to a standstill, delivery dates become wastepaper, and high penalties loom. Early detection of possible failures through predictive maintenance, which is only made possible by retrofitting, is the key factor in ensuring delivery reliability, increasing production output and customer satisfaction.
- Packaging industryThe same applies to the packaging industry, where many machines are connected in series. If one machine stops, the whole line stops. With predictive maintenance, both unplanned malfunctions and planned interventions, such as maintenance measures, can be reduced. In addition, the retrofit of existing lines enables the use of sensor technology for ongoing automated checking of the packaging quality of a wide variety of products, and thus for reducing reject rates.
- Metal production: In the manufacture of metal products, such as tubes, components or car body parts, it is important to detect quality variations in the process at an early stage. The more online sensor technology is used, the more reactive the process control can be designed. In addition, this ensures continuous traceability throughout the entire process. Here, too, the combination of decentralized data recording and central data analysis helps to reduce rejects.
- Surface processingBy using additional sensor technology and combined analytics, wear times for machining tools can be better predicted. This optimizes processes in several ways: highly stressed components in surface treatment can be used for longer and material consumption is reduced, as are downtimes, which has a positive effect on increased productivity.
- Electronics production: Retrofit can use highly complex, AI-assisted inspection methods for early detection of component failures in the production process, thereby increasing productivity rates. They also help to better understand and learn to fix rare special problems.
"Digital retrofit is one of the most important prerequisites and enablers for Industry 4.0," explains Marc Tesch, CEO of LeanBI. "Without this sustainable modernization technology, many valuable and in some cases indispensable legacy systems, production facilities and real estate would be lost to the digital future, along with the associated immense loss of value and resource robbery for expensive, time-consuming new installations."
Source and further information: LeanBI