IoT data room: secure prototypes implemented
The Machine Tool Laboratory WZL at RWTH Aachen University successfully implements secure prototypes for a decentralized, cross-company IoT data space based on the GAIA-X model.
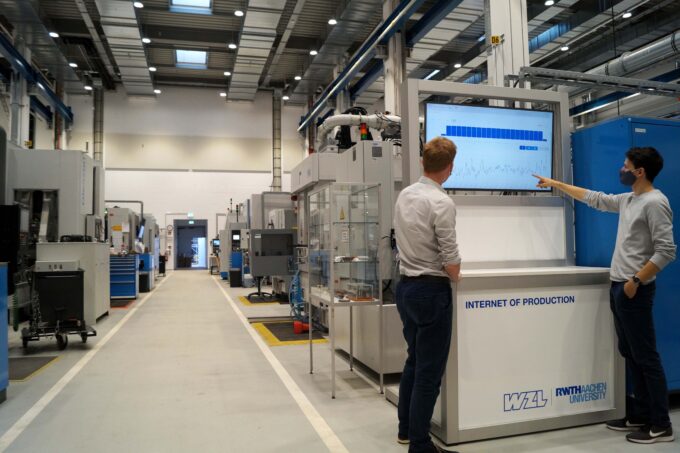
The complete digitization of machines, plants and devices often leads to the creation of data silos within one's own company. However, data silos reduce the quality of the data, hinder internal collaboration and slow down decision-making processes. Not only does the usability of digital assets suffer, but as a consequence, the development of new insights into production processes, the reduction of decision latency and the increase of customer loyalty also suffer.
Next generation of data infrastructure
With the concept "GAIA-X", the German Federal Government, in cooperation with European partners, has developed a proposal for the design of the next generation of a data infrastructure for Europe, which addresses the problems mentioned above. The goal of GAIA-X is a secure and networked data infrastructure based on European values that meets the highest standards of digital sovereignty and promotes disruptive innovation. In an open and transparent digital ecosystem, data and services are to be made available in an uncomplicated manner, brought together and shared in a trustworthy manner.
With these goals as a guideline, the Chair of Manufacturing Process Technology at the WZL Machine Tool Laboratory at RWTH Aachen University, headed by Professor Thomas Bergs, and Senseering GmbH have implemented their own interpretation of a decentralized, cross-company Internet of Things (IoT) data space under the provisional project name "MachineCloud". It enables the seamless exchange of heterogeneous IoT data sources inside and outside the company's own halls, which is why the three WZL sites distributed throughout the city of Aachen were connected to it. The corresponding sites of the neighboring Fraunhofer Institute for Production Technology IPT are also integrated. In addition to its connection to the IoT data room, each of the sites also receives software for visualizing and analyzing the data. The digital assets are thus securely accessible from anywhere and can also be used, viewed and evaluated remotely.
Herman Voigts, a staff member at the Chair of Manufacturing Process Technology at the WZL, explains the advantages of such a cross-company and cross-location data room for fineblanking, for example: "Fineblanking is a highly productive process for mass production. However, the high fluctuation of tool life is responsible for the difficult planning of maintenance and the associated set-up times. We use MachineCloud to increase precisely this plannability, make better use of tool life and avoid scrap production. In this way, we are tapping into a potential cost saving of 30 percent for industrial production. To do this, sensor data is loaded into the MachineCloud, networked and evaluated using innovative methods."
All machines and devices in one digital place
According to the specifications of GAIA-X, data collection and storage is carried out sovereignly in the company's own network. Due to a decentralized architecture, the data owners have sovereignty over the use and release of their own data at all times. Via an intelligent catalogue, all data of other network actors that are in the network and have been released can be actively searched and found. In addition, actors can share their own data with other participants in a systematic and granular manner. For the first time, this enables the joint development of automated and data-driven services based on the shared data. New services are fed back via the IoT data space and thus made accessible to all actors. In the background, a blockchain or distributed ledger technology (DLT) additionally secures the data integrity of any originator data in the entire system and thus ensures seamless tracking of the validity of the data.
"What seemed impossible until recently will now be commonplace: The joint development of AI services on different data sets from different stakeholders for maximum effectiveness in manufacturing supply chains," says Thomas Bergs, Executive Director of the WZL and Chair of Manufacturing Process Technology, who opened MachineCloud at the end of November 2020.
MachineCloud is currently in a pilot phase, which will conclude with the 30th Aachen Machine Tool Colloquium (AWK). On 10 and 11 June 2021, visitors to AWK'21 will be able to experience what it feels like to participate in a sovereign IoT data space according to GAIA-X guidelines and enter into dialogue with the various players.
Press release WZL RWTH Aachen University