Steigerung der Gesamtanlageneffektivität mit Connected Maintenance
Um in einer zunehmend digitalisierten Welt wirtschaftlich kontinuierlich erfolgreich zu sein, müssen auch Unternehmen im Maschinen- und Anlagenbau ihre Prozesse fortlaufend anpassen und optimieren. Auch für Hersteller, die in der Vormontage eigene Produkte herstellen, die in Maschinen oder Anlagen einfliessen, muss es oberste Priorität sein, Ausfälle zu vermeiden. Dabei spielen die Instandhaltungsprozesse, die klassische Maintenance, eine grosse Rolle.
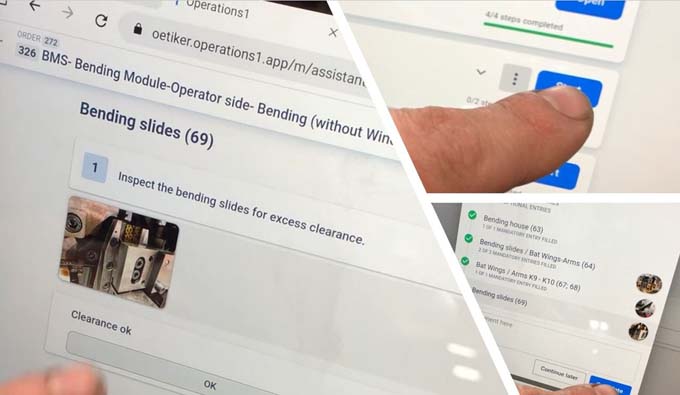
Doch die Implementierung eines Manufacturing Execution Systems allein reicht in vielen Fällen nicht aus. Stattdessen müssen umfassende Lösungen bereitgestellt werden, die nicht nur den Status der Maschinen überwachen, sondern auch den gesamten Instandhaltungsprozess für die Mitarbeiter vereinfachen und diese entlasten.
Die Oetiker Group ist Marktführer im Bereich Verbindungs- und Montagelösungen. Produkte wie Klemmen, Schellen, Ringe und Quick Connectors sorgen für Sicherheit, Leistung und Zuverlässigkeit in Mobilitäts- und Industrieanwendungen. Zu finden sind diese in Pkws, Nutzfahrzeugen, aber auch in Bereichen wie Sanitär und Medizin oder in Haushaltsgeräten. Aufgrund der hohen Qualitätsanforderungen für das breite Produktportfolio ist ein stets einsatzbereiter und jederzeit in Top-Qualität produzierender Maschinenpark unerlässlich. Dafür müssen Instandhaltungsmitarbeitern nicht nur eine effiziente Wartungsplanung, sondern auch anlagenspezifische Wartungsanweisungen zur Verfügung gestellt werden. Zusammen mit der Connected Worker Plattform Operations1 hat Oetiker so seine bestehenden Instandhaltungsprozesse optimieren können.
Status Quo: Vorrangig manuelle Durchführung von Wartungsarbeiten
Wenngleich Oetiker bereits früh eine globale Lean-Manufacturing-Kultur etabliert hat und in allen Produktionsstätten grundlegende Methodiken wie Visual Management, 5S und Total Productive Maintenance einsetze, fehlte zuvor die vollumfängliche Digitalisierung der operativen Organisation. 2020 fiel der Startschuss dazu und das Unternehmen implementierte ein globales Manufacturing Execution System (MES) namens Leading2Lean. Hierdurch konnte eine allererste technologische Kommunikation mit den Maschinen und Anlagen sichergestellt werden, welche Antworten auf grundlegende Fragen lieferte – wie etwa zu Maschinenlaufzeiten, Laufzeitdauer, Unterbrechungen und deren Gründe sowie notwendigen Wartungszyklen. Diese Informationen konnten zwar zur Einrichtung der Instandhaltungszeiträume eingesetzt werden, die detaillierte Planung der Wartungsarbeiten selbst musste jedoch nach wie vor manuell via Excel, Outlook und Magnettafeln durchgeführt werden. Zeit- und ressourcenraubende papierbasierte Instandhaltungsprozesse mit Medien- und Systembrüchen, Intransparenz und erschwertem Reporting waren die Folge.
Die einzelnen Herausforderungen des papierbasierten Instandhaltungsprozesses betrafen in der Tiefe drei Ebenen: das Dokumentenhandling, die Prozessebene sowie die globale Perspektive. Das Handling der Dokumente bestehend aus analoger Erstellung, Freigabe, Überarbeitung, Verteilung und digitaler Ablage war aufgrund des manuellen Ansatzes und der Medienbrüche sehr zeitaufwendig, denn Hunderte von Anlagen bei Oetiker müssen bis dato zu unterschiedlichen Zyklen täglich, wöchentlich, monatlich, halbjährlich oder jährlich gewartet werden. Zudem gibt es maschinelle Varianzen pro Standort. Die manuellen Prozesse konnten diese Vielfalt nicht in der Breite abbilden und so war stets ein potenzielles Fehlerrisiko vorhanden.
Schaffung eines effizienten Wartungsprozesses mit Connected Work
Operations1 erwies sich als passender Sparringspartner auf dem Weg zu einer globalen Digitalisierung der mitarbeitergeführten Instandhaltungsprozesse. Die Wahl fiel aufgrund der nahtlosen Integrationsmöglichkeit mit Leading2Lean, der schnellen Implementierbarkeit an sich sowie der hohen Nutzerfreundlichkeit auf die beliebte Connected Worker Plattform. Darüber hinaus ist die Software-Lösung dank des modularen Aufbaus, der Mehrsprachigkeit und der Möglichkeit, unterschiedliche Maschinentypen durch Strukturklassen im Backend abbilden zu können, äusserst skalierbar. Für die Mitarbeiter der Oetiker Group bedeutet die Implementierung von Operations1 eine erhebliche Vereinfachung der Prozesse ihrer täglichen Arbeit: Nun erhält jeder Mitarbeiter die jeweils für ihn relevanten Instandhaltungsanweisungen zur richtigen Zeit. Zudem erfolgt die Instandhaltung komplett digital mittels intuitiver Checklisten und Prüfprotokollen, bei denen die Werker Wartungsanweisungen Schritt für Schritt über den Touchscreen auf dem Tablet durchlaufen. Auch detaillierte maschinenspezifische Instruktionen können nun digital abgebildet werden. Zudem sind sämtliche ehemals in Papierbergen abgelegten Dokumente in einem Single Point of Truth aggregiert, der zu jeder Tages- und Nachtzeit von jedem Standort aus aktuell abrufbar ist.
Hierdurch wird einerseits die Wartungskomplexität deutlich reduziert und andererseits dank Echtzeit-Prozessdaten und automatisch generierten Reports die Transparenz erhöht. Auch lassen sich dank besserer Planung und regelmässiger Wartung Maschinenausfälle vermeiden. Die gut gewarteten Maschinen bilden nun eine sichere, moderne Arbeitsumgebung für die Mitarbeiter. Ein derart effizienter Wartungsprozess ermöglicht nicht zuletzt eine autonome präventive Wartung: Der Werker kann kleinere Instandhaltungsaufgaben selbst durchführen.
Signifikante Erhöhung der OEE dank digitalisierter Wartung
Bei der vollumfänglichen Digitalisierung der Instandhaltung hat sich Oetiker hehre Ziele gesetzt: So möchte das Unternehmen perspektivisch eine Gesamtanlageneffektivität (OEE) von 85 % erreichen. Diese gilt als wichtige Kennzahl für die Produktivität einer Anlage und eine Steigerung sichert dementsprechend langfristig Umsätze. Um diesen Wert zu erreichen, hat sich der Marktführer Teilziele gesteckt. „Durch einen digitalisierten Instandhaltungsansatz konnten wir bereits nach 6 Monaten die Gesamtanlageneffektivität am Standort Kanada um 11 % steigern,“ so Jacob Reid, Head Engineering, Oetiker Group. Dies geht mit einer Steigerung der Anlagenverfügbarkeit um 5 % einher, während parallel die Mean-Time-To-Repair (MTTR), also die mittlere Reparaturzeit nach dem Ausfall einer Maschine, um 23 % gesunken ist.
Diese Zahlen sprechen für sich und zeigen, dass das Potenzial der digitalen Instandhaltung noch längst nicht ausgeschöpft ist. Bisher wurden 10 von 13 Oetiker-Produktionsstandorten weltweit digital ausgerollt und das Unternehmen hat bereits Pläne für den Roll-out der 3 weiteren Standorte. „Mit Operations1 etablieren wir einen globalen Standard für präventive Instandhaltung in unseren 13 Werken“, bestätigt Susanne Conrad, Head Equipment Engineering bei der Oetiker Group. Die Optimierung der Wartungsprozesse wird also künftig noch weiter an Fahrt aufnehmen.
Quelle: www.operations1.com www.oetiker.com